¿Gestionas grandes volúmenes de cargas con demanda estable? ¿Manejas mercancías perecederas? ¿El tiempo entre que recibes una orden de pedido hasta que se lo entregas al cliente es demasiado largo? ¿Necesitas recortar tus costes logísticos?
Si la respuesta a alguna de estas preguntas es afirmativa, implementar una estrategia de Cross Docking en tu empresa puede ayudarte a mejorar la eficiencia de tu almacén y reducir costes de almacenamiento, distribución y personal, garantizando tus entregas a tiempo.
Sin embargo, su implementación exitosa requiere de una integración y coordinación efectiva entre todos los actores que intervienen en la cadena de suministro, y puede suponer rediseños en el almacén y la adquisición o actualización de un SGA adecuado. Por eso es importante que, antes de intentar emplear esta táctica, conozcas en profundidad en qué consiste el modelo Cross Docking y cuáles son las condiciones necesarias para su implementación efectiva. Una mala sincronización en el proceso podría tener efectos contrarios a los deseados y traer grandes pérdidas económicas para la compañía.
¿Qué es el Cross-docking?
El cross-docking es un sistema de optimización de la cadena logística en el que la mercancía permanece muy poco tiempo en el almacén o se distribuye directamente al cliente final después de su recepción.
Esta transferencia más ágil o inmediata del producto requiere solamente atravesar los muelles de entrada y salida del almacén. De ahí el origen del término en inglés: cross the docks (cruzar los muelles).
En la cadena de suministro tradicional, el flujo entre los proveedores y el cliente final es discontinuo, ya que la oferta y la demanda no están sincronizadas y el almacén retiene los productos hasta que registra una orden de pedido para despachar.
En cambio, en el sistema de cadena de suministro con cross-docking, existe una integración directa entre la oferta y la demanda que reduce el almacenamiento a un tiempo nulo o escaso. Básicamente, podemos simplificar las principales fases de cross-docking en las siguientes operaciones:
1- Planificación de la llegada de camiones con el proveedor.
2- Asignación de muelle de entrada para la recepción de mercancías en el almacén.
3- Descarga, consolidación y control de calidad de cargas, previo a su traslado al muelle de salida (cross-docking indirecto).
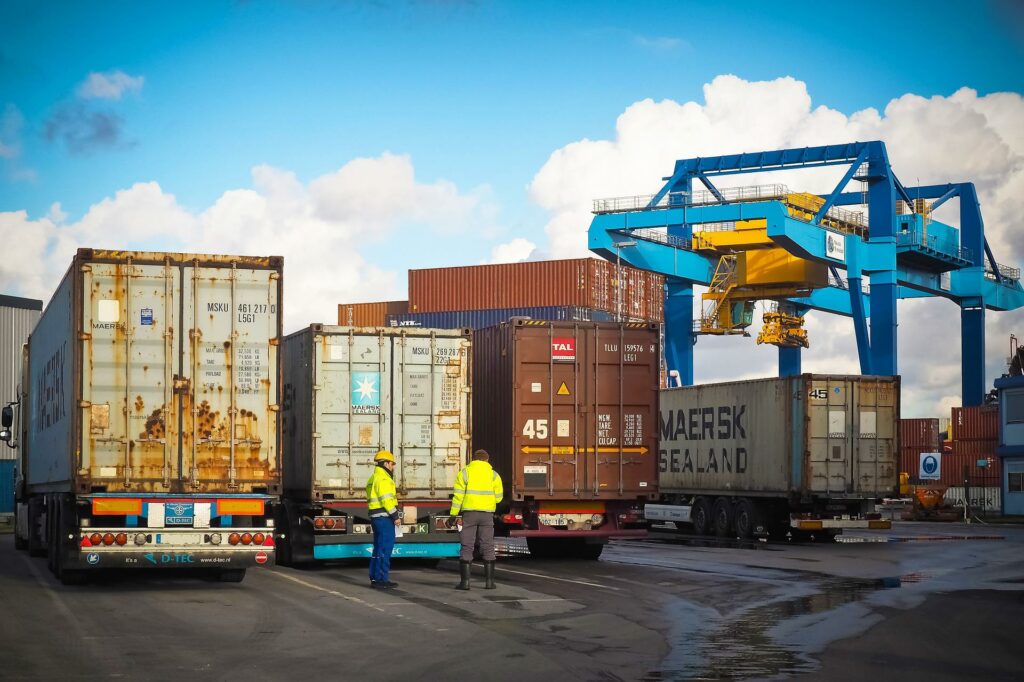
4- Descarga y traslado de mercancías al muelle de salida (cross-docking directo).
El almacenamiento cross-docking permite evitar o reducir al máximo el proceso de inventario y picking de la mercancía, agilizando la rotación de productos, reduciendo costes y riesgos de errores en su manipulación, y mejorando la previsión de entregas.
Tipos de Cross-docking
En términos generales, el cross-docking puede ser:
-Directo/predistribuido: la mercancía llega preparada por el proveedor para que se despache lo antes posible, sin intervención del personal del almacén.
-Indirecto/consolidado: incluye la manipulación de mercancías para adaptarlas a los requerimientos del cliente, previo enviarse al muelle saliente.
-Mixto/híbrido: se preparan los pedidos con las mercancías recibidas y parte de las que ya están en el almacén.
A su vez, existen distintos tipos de cross-docking según el tipo de producto que envíe tu empresa:
- Cross-Docking de Manufactura: este proceso abarca a las empresas que envían insumos requeridos para la fabricación de productos. En este caso, el almacén recibe los pedidos y prepara subconjuntos para las órdenes de producción, previo a su expedición.
- Cross-Docking del Distribuidor: si tu empresa distribuye componentes de varios proveedores, a través de este sistema el almacén recibe los productos de cada uno de ellos para combinarlos en un solo envío al cliente cuando recibe el componente final.
- Cross-Docking de Transporte: esta operación consiste en agrupar paquetes pequeños de diferentes transportistas en un solo envío, para optimizar su costo y lograr una economía de escala.
- Cross-Docking Minorista: este sistema es ideal para cadenas de tiendas minoristas, ya que implica la recepción y clasificación de productos de múltiples proveedores, para su despacho y entrega por lotes en cada tienda.
- Cross-Docking Oportunista: es el modelo más tradicional, aplicable a cualquier almacén. Implica la transferencia directa del producto desde el muelle de entrada al de salida, sin manipulación ni almacenamiento.
Ejemplos de Cross-docking
El cross-docking puede utilizarse para distintos tipos de mercancías y destinatarios finales, ya sean materias primas, productos terminados o componentes de manufactura, expedidos para fábricas, tiendas físicas o consumidores finales.
Sin embargo, existen beneficios específicos para empresas según el tipo de industria a la que pertenezcan, por ejemplo:
- Groceries: los negocios que distribuyen productos alimentarios como los restaurantes, suelen experimentar problemas en su servicio de entrega rápida corriendo el riesgo de que sus productos se echen a perder. Con cross-docking este tipo de empresas pueden asegurarse un flujo constante en la cadena de abastecimiento de alimentos para operar sin inconvenientes.
- Retail: Los retailers demandan flexibilidad e inmediatez, para garantizar una excelente satisfacción del cliente a través de su experiencia de compra. Implementando cross-docking las marcas que ofrecen bienes de consumo pueden optimizar su cadena logística, entregando sus productos ágilmente y reduciendo costes en almacenamiento.
- Healthcare: las organizaciones sanitarias requieren de una gran capacidad operativa para asegurar que sus complejas entregas lleguen a tiempo. Sus productos tienen requisitos de almacenamiento específicos, que los torna caros y críticos al momento del envío. El cross-docking les permite enviar sus productos directamente, reduciendo riesgos de incidencias ante la menor manipulación de los productos.
- Automotriz: esta industria se basa en las entregas a tiempo, ya que el proceso de producción comienza solo cuando se registra un pedido y el stock se abastece a demanda, con lo cual no es necesario almacenarlo y es posible despachar vía sistema cross-docking.
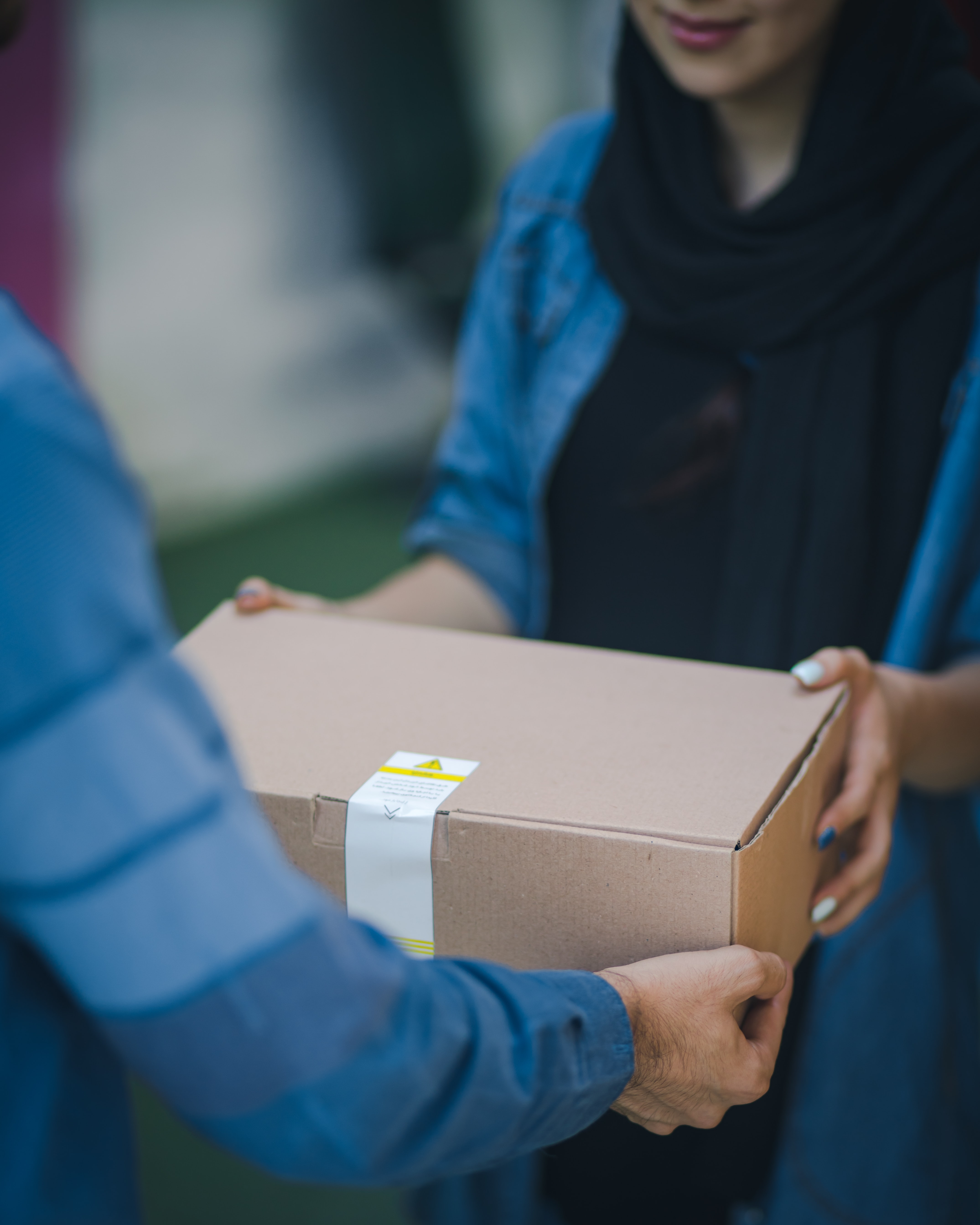
Conclusión
El cross-docking supone numerosos beneficios para las empresas permitiendo ahorrar costos de almacenamiento de inventario y personal, además de agilizar los procesos necesarios para garantizar entregas en tiempo y forma.
Para el éxito de esta estrategia es clave la coordinación efectiva de todos los eslabones de la cadena logística, a través de un sistema TMS adecuado que pueda integrarse fácilmente con los sistemas de gestión de pedidos y de almacenes ya existentes.
Herramientas como VONZU se integran rápidamente mediante API y permiten controlar todas las entradas y salidas del almacén desde un dashboard interactivo, facilitando la previsión de llegadas de mercancías y la gestión de expediciones. Únete gratis.