La logística es el proceso de adquisición, gestión y transporte de los bienes y/o servicios desde el lugar de distribución hasta el cliente final. Este proceso se divide por etapas, permitiendo medir los indicadores de clave de rendimiento (KPI) y optimizar las operaciones de cada fase.
En este artículo aprenderás todo lo que necesitas saber sobre los KPIs en logística y encontrarás una lista de los más esenciales. También te ayudará a entender qué criterios deberás seguir para encontrar los indicadores de logística más adecuados para tu empresa.
¿Qué son los KPI en logística?
Los KPI o métricas de logística son indicadores que te permitirán medir, supervisar y optimizar los procesos logísticos de tu empresa. Estos índices reflejarán la eficiencia de la gestión logística de tu empresa y te ayudarán a eliminar los errores de transporte de mercancías, reducir costes, potenciar la rentabilidad y mejorar la productividad de tus trabajadores.
Estos se pueden dividir en tres categorías o tipos, que se conocen como:
- Indicadores de utilización: Miden cómo se están utilizando los recursos de tu empresa.
- Indicadores de rendimiento: Proporcionan información válida y certera sobre el cumplimiento de los planes de ejecución de las operaciones programadas.
- Indicadores de productividad: Permiten comparar los valores reales obtenidos con los que se esperaba alcanzar en un determinado período de tiempo.
Cómo deben ser tus KPIs
Existen muchos indicadores clave de rendimiento logístico (KPI) diferentes. Los KPIs más interesantes a medir son aquellos que cumplen los criterios SMART. Un KPI SMART es: Específico (Specific), Medible (Measurable), Alcanzable (Attainable), Relevante (Relevant) y Basado en el Tiempo (Time Based).
Para asegurarte que los indicadores que estás eligiendo cumplen los criterios SMART, puedes realizarte las siguientes preguntas:
- Específico: ¿Es tu KPI demasiado amplio? El peligro de tener un KPI demasiado amplio es que la métrica podría ser demasiado imprecisa, lo que podría llevar a interpretaciones erróneas.
- Medible: ¿Es una métrica cuantificable? Recuerda que tienes que establecer un punto de referencia numérico para cada KPI.
- Alcanzable: ¿Es factible el objetivo de tu KPI? Establecer un objetivo que está demasiado fuera de tu alcance desanimará a tus empleados.
- Relevante: ¿Esta métrica responde a una pregunta importante sobre las operaciones de tu empresa? Asegúrate de elegir KPIs que proporcionen información valiosa sobre tu negocio. Hay cientos de KPI que podrían incluirse en tu programa, pero recuerda que tus recursos son finitos. Prioriza tus métricas y elige solo los KPI más importantes.
- Basado en el tiempo: ¿Con qué frecuencia debe medirse cada métrica? ¿Existe un plazo para alcanzar un objetivo establecido? Incluye las respuestas a estas preguntas en la definición de todos tus KPI. Si defines un calendario para cada métrica, este paso será mucho más sencillo.
Con estos criterios, podrás asegurarte de estar eligiendo los indicadores de clave de rendimiento (KPI) que más se adapten a las necesidades de tu negocio.
Indicadores logísticos más utilizados
Ahora que ya conoces estos criterios, te presentamos los principales indicadores logísticos que se usan para medir y mejorar la eficiencia de la mayoría de empresas. Los indicadores logísticos más utilizados son los siguientes:
1. Precisión de los pedidos
Controla el grado de incidencias desde la realización del pedido hasta la entrega de un envío. Ideal para cualquier transportista que busque identificar patrones y corregir continuamente los errores para que el transporte sea más seguro.
2. Puntualidad
Este indicador clave de rendimiento logístico, también conocido como OTIF, mide el porcentaje de pedidos entregados en el tiempo estipulado, sin incidentes ni problemas de documentación.
Es ideal para cualquier transportista que se comprometa a realizar entregas puntuales y seguras.
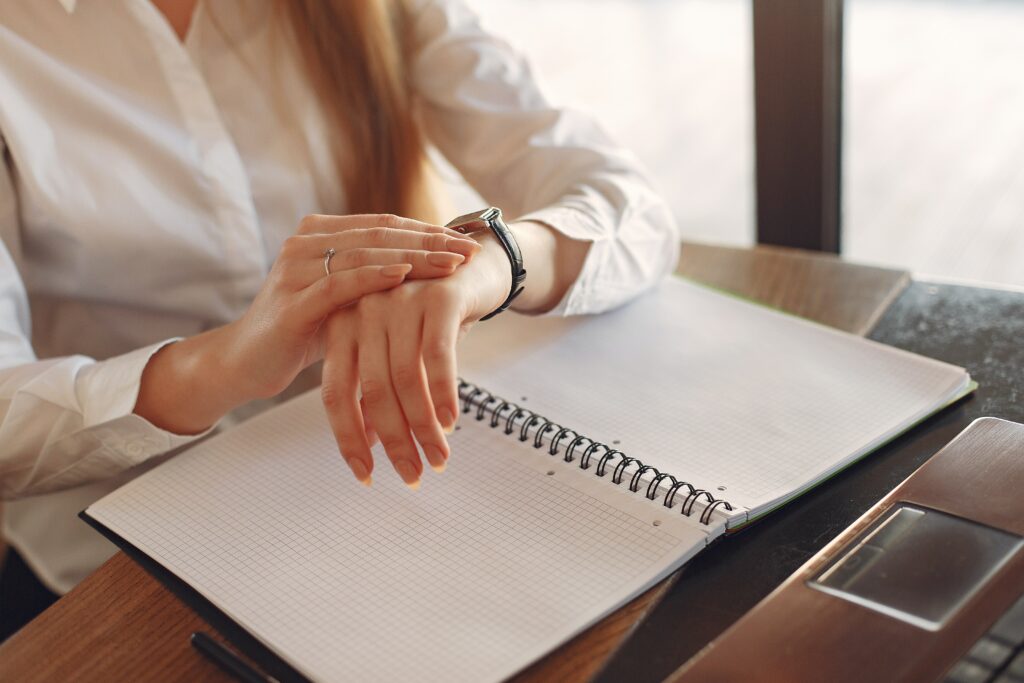
3. Tiempo de entrega
El plazo de entrega es un KPI que mide el tiempo que duran los procesos/operaciones de su empresa, desde el principio hasta el final. Es ideal para que los transportistas conozcan la cantidad de tiempo invertido en cada etapa de la cadena de suministro e identifiquen estrategias para optimizar este tiempo.
4. Rotación de existencias
KPI que hace una media entre las salidas de una empresa con su saldo de stock en el almacén. Ideal para los transportistas que ofrecen servicios de almacenamiento como parte de sus soluciones logísticas.
5. Costes de almacenamiento
También ideal para los transportistas que ofrecen servicios de almacenaje, este KPI monitoriza los gastos implicados en la gestión de las instalaciones de almacenaje de su empresa logística.
6. Utilización de la capacidad
Indicador de rendimiento que mide la utilización de la capacidad de carga de un vehículo durante el transporte por carretera o de un contenedor durante el transporte marítimo. Ideal para los transportistas que ofrecen estos servicios.
7. Productividad
Este rendimiento clave de la logística mide la tasa de producción de los empleados de tu empresa (mano de obra/horas de trabajo/productividad). Ideal para que los transportistas tengan una mejor idea del rendimiento de tu empresa.
8. Costes en transporte
Mide todos los costes relacionados con cada operación logística desarrollada por tu empresa, desde la realización del pedido hasta la entrega final. Este KPI puede ser útil para que los transportistas conozcan la media gastada en cada envío y envíen presupuestos precisos a sus clientes/socios.
9. Número de envíos
Evalúa el promedio de cargas manejadas por su empresa en un período de tiempo estipulado (semanal/mensual/año). Ideal para cualquier transportista que busque hacer balances financieros constantes y analizar sus márgenes de beneficio entre ingresos y resultados.
10. Rotación de camiones
Este KPI mide la rotación de camiones, es decir, el tiempo medio transcurrido entre la salida para la recogida/entrega y el retorno del vehículo a tu empresa.
Es ideal para las empresas que ofrecen transporte por carretera.
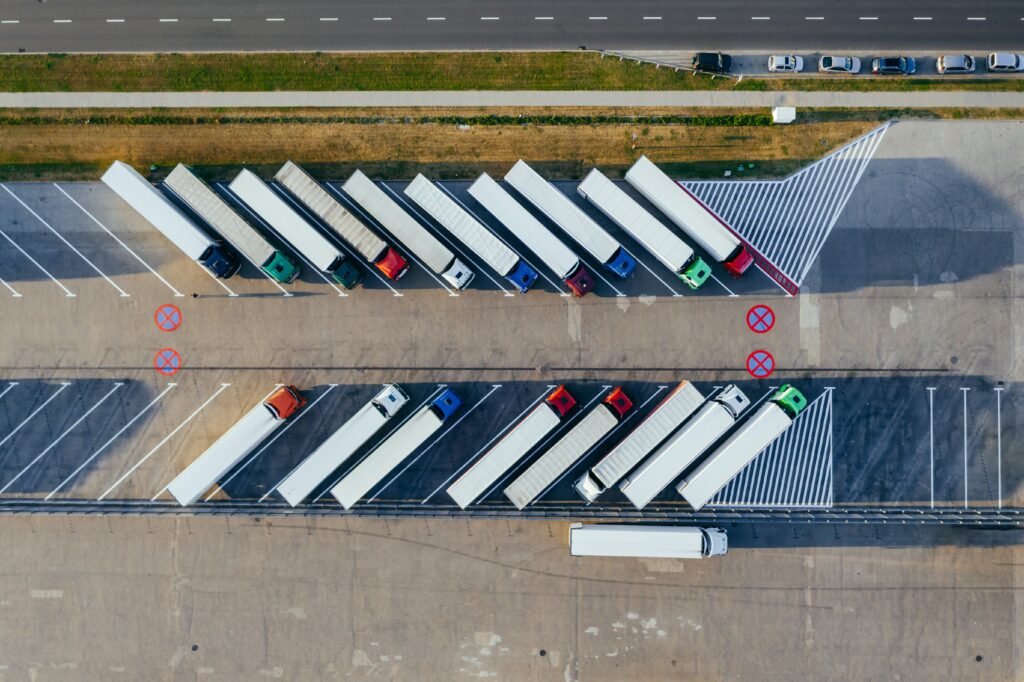
Conclusión
Además de los indicadores clave de rendimiento logístico mencionados anteriormente, hay muchos otros KPI que pueden medir el rendimiento y la productividad de tu empresa en general. Sin embargo, para utilizar los indicadores adecuados, el primer paso es definir qué tipo de datos consideras relevantes analizar.
A partir de ahí, solo tendrás que adoptar los indicadores que te proporcionarán estos datos. Con ellos, podrás reconocer los problemas operativos y crear estrategias que no solo los resolverán, sino que también optimizarán la cadena de suministro de tu empresa.
La logística es el proceso de adquisición, gestión y transporte de los bienes y/o servicios desde el lugar de distribución hasta el cliente final. Este proceso se divide por etapas, permitiendo medir los indicadores de clave de rendimiento (KPI) y optimizar las operaciones de cada fase.
En este artículo aprenderás todo lo que necesitas saber sobre los KPIs en logística y encontrarás una lista de los más esenciales. También te ayudará a entender qué criterios deberás seguir para encontrar los indicadores de logística más adecuados para tu empresa.