Imagínate que un cliente te encarga unos zapatos nuevos para asistir a una comida familiar de Navidad. Consigues entregar el paquete justo a tiempo pero al cabo de unas horas, el cliente empieza un proceso de devolución porque ha recibido la talla equivocada.
Las devoluciones se han convertido en un desafío único para las empresas que participan en el mercado del comercio electrónico. A nivel mundial, los compradores devuelven aproximadamente US$642,6 mil millones en mercancía por año, según un estudio de ComScore.
Aunque parezca que el proceso de devolución sea un pequeño componente de las operaciones de transporte, el no gestionar adecuadamente los desafíos que propone la logística inversa puede afectar significativamente a la rentabilidad de tu negocio.
¿Qué es la logística inversa?
La logística inversa es un proceso de gestión de la cadena de suministro que consiste en devolver los bienes o servicios de los clientes a los vendedores o fabricantes. La mercancía final retrocede, como mínimo, un paso hacia atrás dentro de la cadena de suministro. Este viaje de productos o servicios en sentido inverso, es el que da nombre a la logística inversa.
Cualquier proceso o gestión posterior a la venta del producto o servicio implica una logística inversa. Este proceso puede incluir las devoluciones de productos, el reciclaje y los cambios.
¿Cómo funciona?
La logística inversa varía según diferentes sectores. El ejemplo de logística inversa más común es cuando un consumidor devuelve un artículo comprado para su reembolso y posteriormente pasa a ser revendido, reciclado o eliminado definitivamente. En general, el proceso sigue cinco fases:
1. Devolución del artículo
Cuando un cliente quiere devolver un artículo, se pondrá en contacto con la empresa. El paquete será enviado de nuevo al almacén o al centro de procesamiento. A continuación, la empresa autorizará su reembolso o sustituirá los artículos defectuosos para poder enviarlos de nuevo.
2. Selección de los artículos recogidos
Se realiza una revisión e inspección de los embalajes recogidos y reparados.
3. Reparar, organizar y clasificar
Respetuosa con el medio ambiente, esta fase de la logística inversa es una de las más valiosas del proceso y te permitirá ahorrar a largo plazo.
4. Reciclaje o incineración
Algunos productos llegan al final de su vida útil. Si no pueden ser reparados, reutilizados o remanufacturados, estos pasarán a ser reciclados o eliminados.
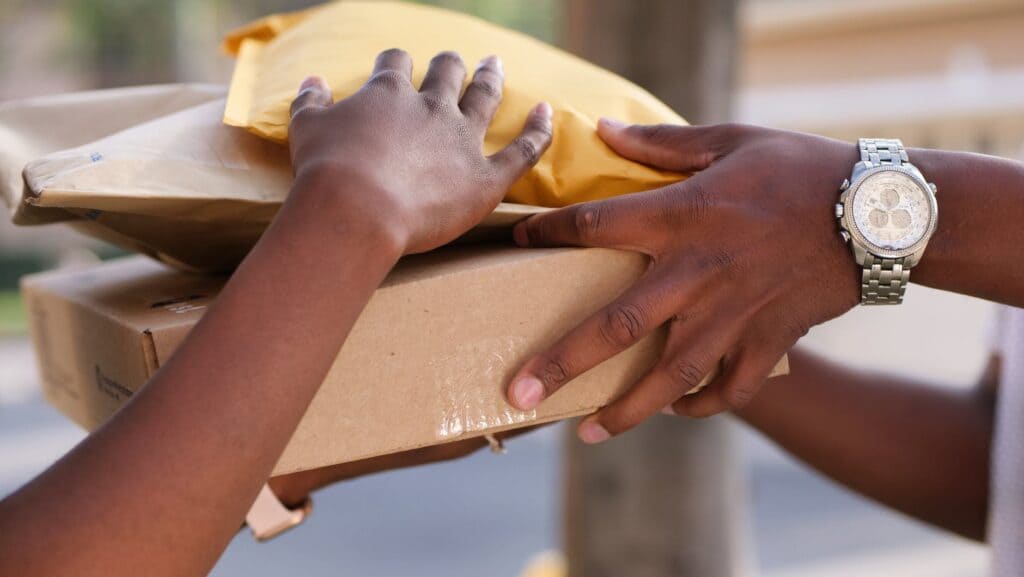
5. Procesar, organizar y clasificar
Se prepara todo para el envío del nuevo artículo para el cliente.
¿Cuál es su importancia?
La logística inversa es importante porque mantiene la eficiencia de la cadena de suministro. Este proceso tiene muchos beneficios, los cuales enumeramos a continuación:
- Ahorro de costes: Con un sistema de logística inversa implementado, ahorrarás gastos innecesarios. Si descuidas este proceso, es probable que se produzcan costes desorbitados en tu empresa relacionados con el transporte y el almacenamiento.
- Satisfacción del cliente: Tener un proceso de devoluciones rápido y fácil aumenta la satisfacción y la retención de los clientes.
- Sostenibilidad: Con esta práctica, las empresas participan en un sistema centrado en una economía sostenible. El reciclaje y la reutilización de materiales usados no sólo es beneficioso desde el punto de vista económico, sino también para el medio ambiente. Estas políticas de sostenibilidad aumentarán tu reputación.
- Valor de la mercancía: La logística inversa te ofrece la oportunidad de conservar un valor para tu empresa que de otro modo se habría perdido. Al reutilizar y encontrar nuevos usos a productos que podrían haberse convertido en residuos, podrás generar más ingresos.
- Obtén información para tu negocio: Un proceso de logística inversa bien organizado te proporcionará datos valiosos para tu empresa. A través de softwares de logística como Vonzu, podrás analizar los motivos por los que se devuelven los productos, abordar los problemas que los causan y mejorar las decisiones estratégicas de negocio con esta información.
Ejemplos de logística inversa
En los siguientes ejemplos de logística inversa veremos algunos de los métodos que utilizan las empresas para gestionar correctamente los productos devueltos:
Devoluciones
Tu cliente podría comprar un artículo por error o seleccionar las especificaciones incorrectas. Gracias a una política de devoluciones, darás la satisfacción del cliente de saber que obtendrá sin problemas aquello que ha pedido y es más probable que te vuelva a comprar.
Reutilización
Algunos productos y/o materiales son recuperados para volver a reutilizarse. La reutilización se diferencia del reciclaje porque los materiales no se someten a ningún otro proceso. Un buen ejemplo son las empresas de alimentación y bebidas que reutilizan cajas, botellas y barriles. También hay negocios que permiten alquilar productos durante un período determinado para después ser devueltos y usados por otro cliente.
Reparación
Si un producto se estropea en un plazo determinado después de su compra, los fabricantes pueden ofrecerse a repararlo. El objetivo siempre será devolver el producto a su estado original. Algunas empresas incluso ofrecen servicios de mantenimiento, retirando las compras cada cierto tiempo para mantenerlas en buen estado.
Remanufactura
La remanufactura es un proceso por el cual se transforman los productos que han llegado al final de su vida útil en productos parecidos al usado, pero con una nueva vida, calidad y garantía.
Reciclaje
Los productos pueden llegar al final de su vida útil, y en ese caso no se podrán ni reparar ni reutilizar. Si un artículo se ha estropeado (o ya no sirve), es probable que el cliente quiera deshacerse de él. Algunos fabricantes ofrecen recoger estos materiales para reciclarlos.
Incineración
La incineración también forma parte de la cadena de logística inversa, pero tiene un papel mucho menor, ya que las empresas buscan formas de revender, reutilizar y reciclar sus productos devueltos. La incineración suele utilizarse como último recurso.
Conclusión
La logística inversa puede ser todo un desafío pero si comprendes cómo funciona este proceso, te asegurarás que tu empresa saque el máximo rendimiento de este sistema tan necesario.
Recuerda que un software de logística como Vonzu te permitirá tener un control exhaustivo de tu almacén y hacer más eficiente tu proceso de devoluciones.
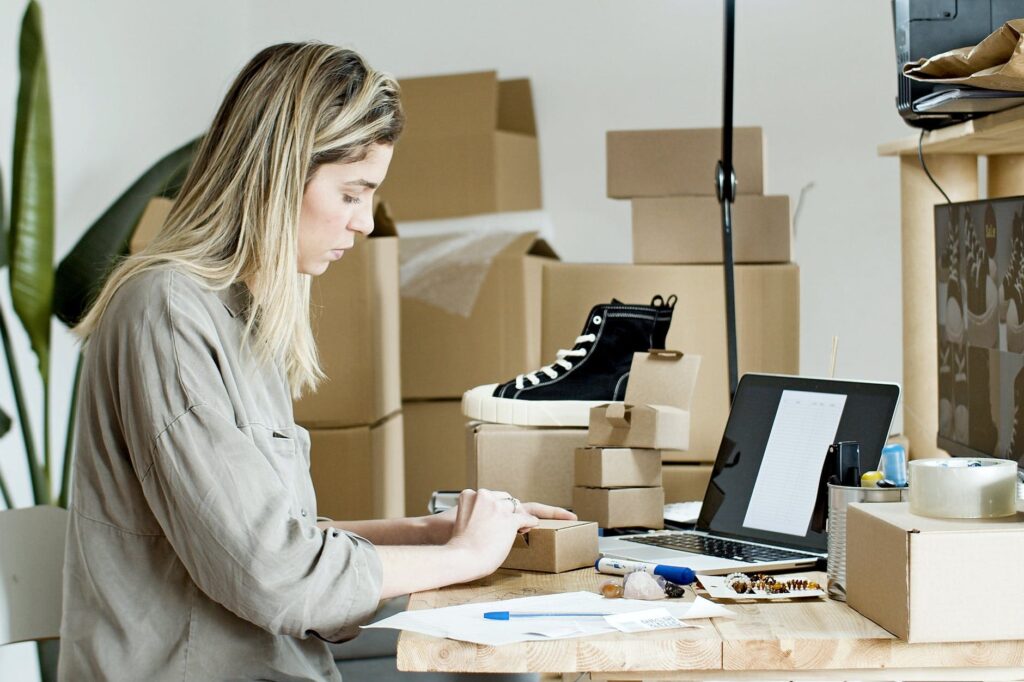